In geography / geology during our school days, we often learn about different types of stones. It makes us wonder why they call diamond the hardest stone, or if it is a stone at all. It looks so different from all the other stones around it. A few weeks before our Gujarat trip, we saw an old documentary (The Diamond Empire) on diamonds, which spoke about them being artificially priced high due to the monopoly of De Beers. But the monopoly was broken several years ago, and nobody heard of a glut in the diamond market or any significant fall in the prices. It was intriguing. And then there we were in Surat. So after calling a few people in the family who are diamond merchants, they generously arranged for a factory visit for us.
That is how we landed up in the factory of Blue star Diamonds,one of the biggest diamond cutting factories in Surat, the diamond city.
Diamond cutting and Surat
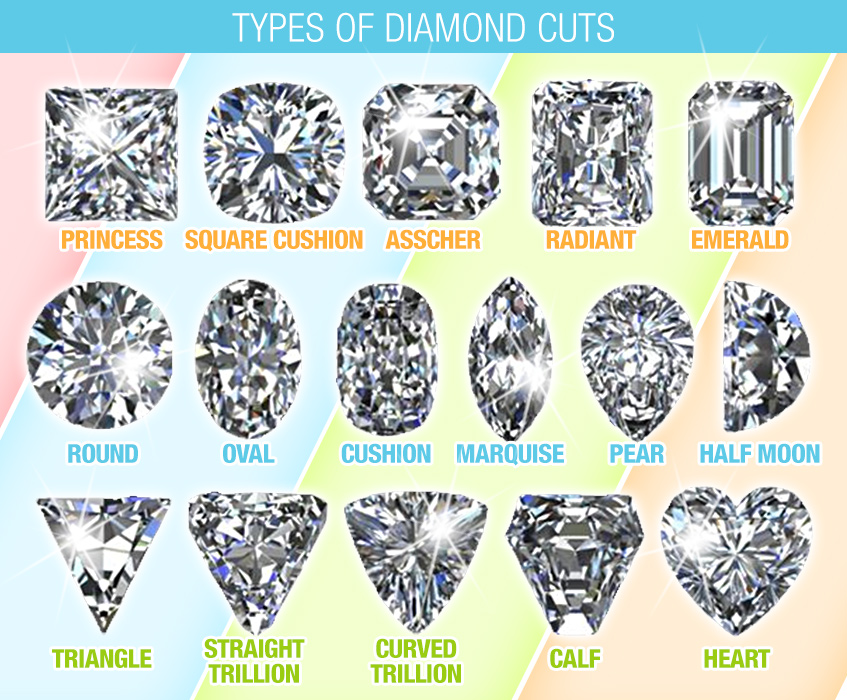
Diamond- Types of Cuts
Surat processes almost 90% of the diamonds in the world. Cutting and polishing of diamonds is an extremely intricate work. That process is done by highly trained professionals. Since the 1960s Surat has been a hub for the diamond cutting and polishing. Generations of merchants now know the secret to buying and pricing the world’s best diamonds. And several artisans have learnt the skill of cutting, shaping and polishing diamonds in a way that very little of the precious stone is wasted.
The documentary that we watched was produced and released in late 1990s. It shows sweatshop factories in which scores of people are lined up and hunched over a microscope with some tools. But what we saw in the modern factories of Surat was nothing like it. Having worked in IT industry for over a decade, swanky offices are not new to us. But this was the first time, we saw a super swanky factory. As expected, there was heavy security and cameras everywhere.
Our visit
We had an appointment with Riken Shah, who was in charge of the operations in the factory. The security let us in after checking our credentials and that we indeed had an appointment. Casual visitors to the factory were not common and the security seemed both surprised and reluctant. Both the inside and outside of the office was comparable to any IT office. In the myriad of cabins, we managed to find Riken Bhai who introduced us to his manager, who was to take us on a tour of the factory and show the various processes.
While we were having tea, one person came into the cabin, pulled out a white sheet containing a set of sparkling diamonds. In the next few minutes, they were discussing about whether it was worth further processing these diamonds to enhance their value. Riken Bhai decided it was not. The man put the diamonds back into the sheet, folded the sheet and put it into his pocket before leaving. Like a magician pulling a rabbit out of a hat, everybody seemed to be pulling diamonds out of their pockets. Throughout India 360, we had been so sloppy with our phones, cameras and keys so many times that we didn’t want to go anywhere near a simple paper sheet containing diamonds and risk spilling them all over the place.
The diamonds are imported from various mines in Russia and Africa by De Beers, a consortium that owns the majority of the mines and controls much of the trade. The imported stones are allotted to the various cutting factories based on their capacity, requirement, contract validity and several such factors by De Beers. Each diamond goes through a sequence of 36 processes from the time it is imported. To name a few, each diamond and a batch of similar diamonds is tagged with computerised IDs, diamonds are measured, cut and polished and the final product is certified and ready for market. Let’s see a few processes that we had the opportunity to see in person and find details about.
Planning Unit
Our Tour started with the planning unit. Once the diamonds are taken up for processing, each one is individually evaluated on what’s the best way to cut with the least amount of wastage to the stone, so as to derive the maximum value out of it. The raw stone dimensions are fed into a computer running a specialised 3D imaging software. This software comes up with some suggestions on where to make cuts in the stone. The price of the software runs into several crores (tens of millions) and the operators are trained in using them. The suggestions made by the software are manually verified and improved if necessary. These designs are then submitted to senior design team for their review and approval. If they believe that the design can be improved upon they send it back for rework with suggestions. Each session of the design for a single stone lasts 4-6 hours. The employees do not take breaks during this time as it may hamper the flow of the process. They do it all in a single sitting. They certainly follow the maxim: Measure twice, cut once.
First Cut
After the planning stage is done, the first broad cuts to the stone are made. The biggest diamond(s) take maximum priority during the design phase, as bigger diamonds get a far higher price than smaller ones of same specifications. The smallest diamonds they cut are the ones that are usually used in watches. This cutting is a power intensive process that is completely automated by machines using LASER to cut the hard stones. The machines are imported from Netherlands and Israel and cost several crores. The more advanced machinery can cut to greater precision thereby limiting the wastage. Reduction of wastage by a even a single % can be huge in this industry.
Second Cut
Once the broad cuts are made, the diamonds are then assigned to different units for a final cut. Yet again the designs are analysed and finalised before the cut is made. The units here are broadly classified based on the type of cuts. Type of cuts are broadly classified into square, round and special shapes like heart, triangle etc.
Specilized Manual Cutting
When the team feels that a stone is too fragile and that a machine cut risks further damage, or if the design is too intricate, they send it to be cut and polished manually. Employees in the unit have well over 10 years of experience and handle the finest of cuts and most fragile of the stones. The wastage is calculated unit wise and analysed thoroughly to keep it under check.
Demand Driven Designs
So far we have talked about how the type and quality of stone dictates the type of cut it receives. But demand also plays a good part in deciding what kind of stones with what cuts will be produced. Every week they receive a market report from Global Industry Standard ‘Rapaport’ which provides details on the demand and supply. The team tweaks their designs to meet the numbers based on the report as that is also an important component to maximise the revenue per stone.
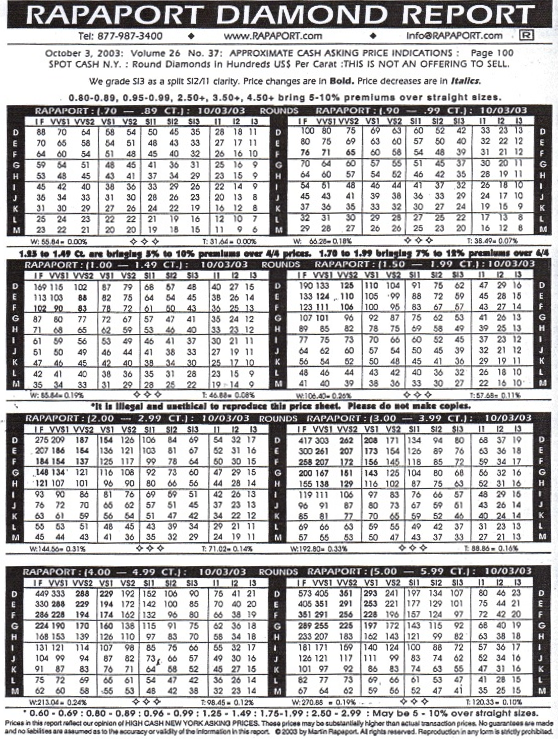
Rapport diamond Report
After the tour
We were shown some final cut diamonds and the manager even generously asked us to hold some of those glittering stones. But we declined, refusing to be the reason for crores of Rupees in losses due to sloppiness or clumsiness.
We met Rikhen Bhai after the factory tour. Riken was just over 30 and the head of such a massively complex operation handling several crore Rupees of expenses, income and profits. He admitted that he had finished school with bare minimum grades and has been in the diamond cutting industry for several years. He is proud of how the industry has evolved and the kind of job opportunities it provides to the vibrant hardworking youth in this town. He said proudly, ”Most workers here have completed only their 8th year of school before dropping out. But they earn ₹ 50,000 per month. We provide good employment and medical benefits. Tell me about any other industry that can provide this standard of living for people with the level of formal education that is usually considered inadequate. I myself am an example of such a success story of this powerful diamond industry in Surat.”
Conclusion
We ended our tour with a sumptuous Gujarati Thali prepared in the factory’s kitchen. Also with us were some of the factory’s workforce, including an apprentice from Israel. The visit certainly made us appreciate the volume of work that goes into the tiny works of stone that both of us wear on our ring fingers to symbolise our marriage and long-term commitment, a relation that we consider to be strong and aptly represented by the hardest stone on the planet. Can’t say if ‘Diamonds are forever’, but the memories from the visit to a diamond factory certainly are.
Very interesting article & explained things in the best way. Would like to connect with the author.
Thank you so much Riken ji for hosting the tour for us and for the comment. Will reach out to you over the weekend. 🙂